The Advantages of Block Diagrams in Industrial Process Controls
Whether you’re designing a new system or making improvements to an existing one, a block diagram is a great tool to leverage when communicating a high-level overview of the relationship between the system’s various major components and processes. While block diagrams may not include everything in a system down to the smallest circuit, they are a valuable resource when designing industrial process control systems. The purpose of this article is to provide insight into block diagrams and the reasons why they are well suited for industrial controls.
What is an Industrial Block Diagram?
Admittedly, the meaning behind the term “block diagram” isn’t intuitive to anyone outside of the engineering discipline. Despite this, block diagrams facilitate the development of many of the systems and processes that society relies upon. Block diagrams are specific, high-level diagrams that are used to provide a high-level overview of how a system’s (and/or processes’) various components, devices, etc. relate to one another. If this sounds difficult to visualize, think of a company’s organization chart. You may have one block identified as “corporate” under which you’ll likely find branches to separate blocks for human resources, IT, and accounts payable. The corporate block may also branch off to a manufacturing block, and so on. Again, the purpose of a block diagram, like an organization chart, is to illustrate the relationships between the various blocks, rather than communicate any kind of rigid flow processes.
Put more simply, block diagrams offer up a quick view of an overall system or process that helps designers and decision makers identify potential issues or previously unconsidered opportunities before physical construction begins. It’s important to understand that a block diagram will not illustrate everything right down to the level of an individual circuit (in fact, another document, called a circuit diagram, provides that information at a granular level). Instead, the high-level overview provided by block diagrams tends to focus more on the input signals relayed by the PLC and output actions executed by the field devices. Block diagrams display the system at such a high level that they can generally be laid out on a single sheet of paper. This is beneficial when it comes to explaining how the system works to individuals joining the project or those with less industry experience.
Improves Visualization and Understanding of a Complex Control Process
Industrial systems can be incredibly complex; however, block diagrams facilitate the explanation of these systems by focusing only on the principal elements of said system. Namely:
- Inputs and outputs (I/O)
- Functions
- Processes
- Devices
Interestingly, block diagrams will generally omit specific system or process details that are not relevant to providing the reader with “an overall perspective”.
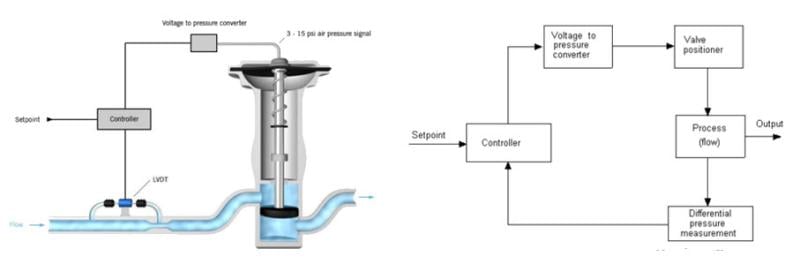
Easy to Construct Even for a Complicated System
Constructing a block diagram, regardless of the complexity of the system, can be a relatively simple task, provided the following criteria are observed:
- The descriptions representing the associated block effectively communicate the function performed by the device, process, etc.
- “Blocks” should represent a process, function, transformation, or activity. Not only does this keep the system diagram to a high level, it also provides the information necessary to develop an understanding of the system.
- Connector lines are used to represent the inputs and outputs that “connect” or relate to other function blocks.
- Depending on the system and the information required to communicate by the block diagram, each function block can have one or more inputs and outputs associated with it. A designer may choose to represent a complex process or system with a single function block if they’re able to adequately summarize the operation. Alternately, they may choose to break up the operation into many blocks, each with their own I/O.
- During the design phase, block diagrams are used to identify and create the functions that will be needed to complete the process, and they also provide the opportunity to document the variables and signals that will require definition by functional specification documentation.
- The functional specification documentation is then used to provide developers with clear, concise, and complete information pertaining to the various components used in the system. This could be anything from enumerating heat tolerances, voltages, upper and lower ranges, and loading limitations, to name a few.
A Diagram to Simplify Processes
It’s interesting and useful to know that even the most complicated systems can be visually represented by a series of blocks representing functions, I/O, processes, devices and more. Perhaps more interesting still, is that these diagrams are useful both at the earliest stages of conceptual design and after system completion. If you would like to learn more about how block diagrams are used in industrial process control applications, be sure to check out the courses available at George Brown College today.